About us
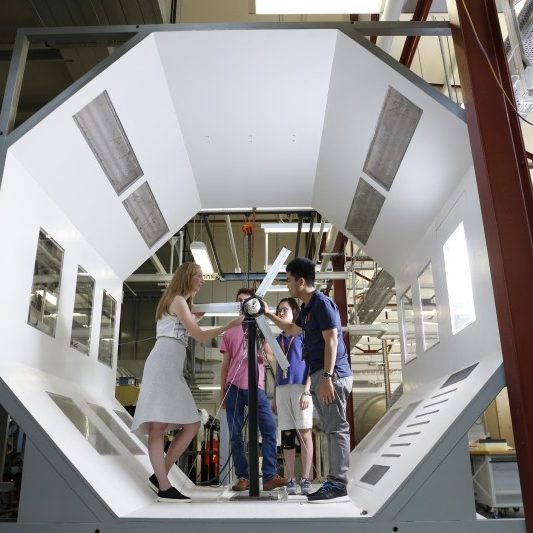
We are a large and lively team of academics, postdocs, postgraduate and honours students based in the School of Mechanical and Manufacturing Engineering at the University of New South Wales, Sydney. We have strong links with academia, government and industry which provides endless inspiration for new research and provision of high-quality education.