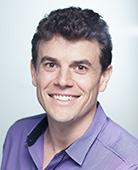
Professor Garth Pearce
I am a Professor in the School of Mechanical and Manufacturing Engineering, specialising in the mechanics and design of composite structures. My research exploits both simulation and experiment to explore the multiscale mechanics of composite materials. I investigate the relationships between composite constituents, manufacturing methods, microstructure and structural properties. With this knowledge, my research team build tools to efficiently design composite structures for improved structural integrity, stability and response to extreme conditions. A strong industry connection is fundamental to my research. I have fostered relationships with organisations across the composites manufacturing sector (Boeing, Lockheed Martin, Omni Tanker) as well as defence and national research organisations (DST Group, ANSTO, German Aerospace Centre). I develop material models and design tools which my partners are using to shorten product develop cycles and reduce design risk. |
- Publications
- Research Activities
- Engagement
- Teaching and Supervision
![]() Multiscale Modelling of Composite Materials and StructuresStrength prediction in composite materials is fundamentally linked to the mechanics of their micro- and meso-structures. My research widens the design envelope for composite materials by combining interdisciplinary theoretical, analytical, numerical and experimental approaches. I have delivered advances in tomographic visualisation, simulation and analysis of textile composite structures. My group pioneered novel approaches to visualise damage evolution in multi-material composite systems, such as fibre metal laminates using X-ray and neutron tomography. |
||
Automated Manufacture of Advanced CompositesI am a Chief Investigator of an ARC Training Centre for Automated Manufacture of Advanced Composites (AMAC). My project has developed novel modelling strategies for the complex geometric discontinuities in AFP and filament wound structures and enabled optimisation of AFP manufacturing processes. |
||
Composite Vessels for Dangerous Goods TransportWith research partners Omni Tanker and Lockheed Martin, I have developed simulation and analysis tools for the development of CFRP dangerous goods transport vessels (Type IV and V) for room temperature and cryogenic applications. I have been involved in the design and development of three commercial transport vessels for export markets and prototype linerless cryogenic hydrogen vessels. Integral surge protection technology developed with Omni Tanker has been certified and deployed across multiple product lines in global markets. |
||
|
Impact on Industry Products and Processes
Research translation is fundamental to my research objectives. Wherever possible, I strive to apply my work to real industry challenges.
My team have developed a plugin for Abaqus finite element software which encodes the main theoretical findings of the two consecutive linkage grants into a parametrizable user interface.
My research and research supervision have contributed to the design and development of three Omni Tanker products and $1M in grant success for this Australian SME. The first trial collaboration, an AMSI Internship, led to the development of the L4 Mini Tank and the long-term employment of the PhD intern at Omni Tanker. I was then invited for sabbatical in 2018, when I led engineering design efforts for the layout, shell and crash protection for the US Road Tanker which included using innovative software tools developed in my team. This product has just left development and the first units have been launched in the United States. During the same secondment, I wrote a successful proposal for a $1M Global Innovation Linkages (GIL) grant to develop two new products.
UN Model Regulations for Dangerous Goods Transport
Omni Tanker are leading a UN panel to redevelop the UN Model Regulations for Dangerous Goods Transport Vessels to incorporate improved regulation of composite vessels. My research expertise (composite failure theories, strength and damage characterisation, composite manufacturing, etc) has contributed to Omni Tanker’s accepted draft proposal to this panel. The UN Model Regulations, once formally ratified, will promulgate to many international jurisdictions and will govern the regulation of composite dangerous goods vessels into the coming decades.
My Research Supervision
I have projects in the following areas:
- Modelling textile composites from advanced tomography
- Micromechanics of composite degradation and failure
- CFRP cryogenic liquid tanks for Hydrogen transport
- Lifetime assessment of bonded patch repairs
- The manufacturing of aerospace components using AFP: a study of materials, in-process defects and failure analysis
- A tow-wise modelling approach for non-traditional AFP laminates
- A novel continuum mechanics approach for the interfacial response of orthotropic composite materials
- CFRP antarctic wind turbine
My Teaching
I am Deputy Head of School (Education) for Mechanical and Manufacturing Engineering at UNSW.
I convene high level disciplinary and elective courses in Mechanical and Aerospace Engineering. My courses encourage research, open-ended problem solving, critical thinking, as well as personal and peer reflection.
I currently teach:
- Finite Element Methods
- Aerospace Structures
- Composite Cryotanks (Vertically Integrated Project)